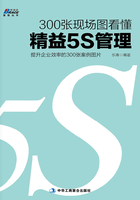
5.为什么丰田只做4S管理,我们却冲刺10S(3)

图1-20 丰田物流输送车
丰田物流输送车将物料按需要的数量在需要的时间送到需要的地方。不多给物料,避免造成生产现场堵塞,导致寻找、搬运等时间与人力的浪费。很多企业的物料员巴不得把一个星期的物料都拉去生产线,然后物料员就可以悠闲地玩手机。殊不知这样做会造成生产现场空间被占用,各工序操作被堵,导致无用的搬运,降低生产效率及产量。笔者认为罪魁祸首不是物料员,而是管理者意识不到、识别不了,这是重大的浪费。笔者通过对丰田的货架讲解,请大家思考5S管理服务的对象到底是谁。
大家看图1-21的货架,货架是存放待组装汽车零部件的。货架每层都有斜坡——省力化。送料员把装满物料的塑料筐放在斜坡上;货架对面的操作工移开空塑料筐后,装满物料的塑料筐会自动滑到货架的另一边,方便操作工拿取,操作工不需要搬运。操作工把使用完的空塑料筐放在最底层,塑料筐会自动滑到货架的另一边,方便物料员取回空塑料筐,这个过程也不需要搬运。

图1-21 丰田的货架(1)
看图1-22、图1-23、图1-24,每个货架的形状都不一样。很多人会奇怪为什么不统一货架,这样才好看、美观?这是错误的5S管理观念。做5S管理的时候一定是效率第一、美观第二。丰田装配现场的货架是根据存放物料的形状大小设计的。换句话说,货架是服务摆放的物料,目的是方便拿取、提高效率。如果货架都是统一大小、高度、层数,存放物料肯定不好放、不好拿、不好管理,效率就低。

图1-22 丰田的货架(2)
以前培养过我的一位在丰田工作过18年的精益专家说过:“丰田建新工厂,工期是3年,可能前2年都在做计划,第3年才开始动工。”
做什么计划呢?大到各车间与各车间的布局,布局流畅,生产过程才会减少搬运次数、动作等无用功;中到根据计划产能,做好车间各种设备的选型及软件模拟仿真演练;小到每个工序用什么货架、用几层、每层需要什么尺寸的盒子都列出来。这些计划做好之后,模拟仿真,反复地计划、实施、检查、总结。循环(PDCA)没问题,第3年才开始实施,这样基本可以一步到位,因为前期经过了多轮演练、检查、总结。很多企业开工了又返工,边施工边修改图纸,这样做成本很高。施工之前可以考虑先模拟演练几遍,避免后面返工造成巨大损失。
图1-25中有提到工具使用点检,那么为什么要每周点检工具?看笔者总结的一个公式:

图1-23 丰田的货架(3)

图1-24 丰田的货架(5)

图1-25 变化点管理板
需要工具找不到→(生产等待+设备等待+相关人员等待+物料等待)→产量降低→人均效率低→成本增加→企业竞争力下降。
丰田平均60秒组装出1辆汽车,哪能允许花1分钟找工具?很多企业换产、换模具,维修找工具就超过1分钟,太浪费了。
笔者观察过一些民营企业,有的甚至是上市企业,他们的工具是怎么管理的?大多是仓库管理,领用的时候登记,规定1个月检查1次,结果3个月都没检查。最后大检查,很多人的工具都不齐全。试问,这样如何满足日常使用?
很多企业都在考核设备停机时间,但没有几个企业真正分析过设备停机时间到底由什么组成。比如停机报表上写着××设备停机60分钟,如果只看报表,就会认为设备停机了60分钟。其实设备没有停60分钟,而是被人无意识地延长到了60分钟。
下面笔者模拟设备停机都有什么工作要做:
①设备停机→②操作工报修→③维修工到现场→④开始维修→⑤维修结束→⑥开机试运行。
上面的流程中,设备停机后,操作工报修给维修工是以什么方式报修,打手机、内线、对讲机?用了多长时间?
描述设备停机问题是否清晰?不清晰会导致维修工没有带足够工器具或者备用品过来,需要折返。整个流程中浪费了很多时间,最终汇总成设备停机60分钟。
言归正传,丰田把工具这个关键物品纳入日常检查。
丰田的班组长每天都有固定的关注点,对安全、品质、生产、成本、人事、环境、设备保全都有明细,如表1-1所示。
表1-1 工具点检内容


这样的标准化工作内容不仅能帮助班组长梳理工作重点,还能帮助新上任的班组长快速掌握工作重点,以及未来传承整个文化。
丰田现场的情报屋也叫大部屋(如图1-26所示)。把生产相关的资料、信息全部目视化出来,让全员都知道、了解,以便快速做出反应。避免信息被少数几个人掌握,万一这几个人请假、休息或者忘记了,车间信息就流动不起来,就会出现各种问题。

图1-26 大部屋