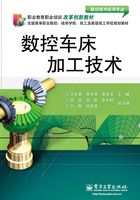
任务五 数控机床的应用与发展方向
任务描述
普通机床和数控机床的选用原则?如何合理利用数控机床加工相应的零件?数控机床发展从哪些方面着手?
学习目标
了解数控机床应用范围,掌握数控机床的谈谈方向并能联系实际谈谈我国数控机床的发展。
任务分析
合理利用数控机床是使加工成本利益最大化的必要条件,只有了解数控机床的应用和相应的发展方向,才能更合理地选用数控机床。
任务完成
数控机床发展至今已有四十多年的历史了,它与电子技术,特别是计算机技术的发展密切相关。自世界上第一台数控机床在美国麻省理工学院研制出来后,数控机床在制造工业,特别是汽车、航空航天及军事工业中被广泛应用,数控技术无论在硬件还是在软件方面,都有飞速的发展。随着现代经济和科学技术的飞跃发展,尤其是计算机数控系统的出现及微型计算机的迅速发展,再加上数控技术的普及和电子器件成本的降低,这些有利的条件都使得数控机床的应用范围越来越广泛,其加工成本不断降低,加工精度不断提高。数控系统除了用来控制金属切削机床外,还普遍用于控制诸如冲床线切割机、简单机器人之类的复杂设备,在要求可靠性和高柔性强与实现机电一体化等方面的生产加工中对数控机床都有广泛的需要,由于数控机床属于精密设备,致使成本较高。因此,目前多用于形状复杂精度要求高的中小批量零件加工。
一、数控机床的应用范围
一般来说,数控机床特别适合于加工零件较复杂、精度要求高、产品更新频繁、生产周期要求短的场合。数控加工适用范围可用图1-1-8粗略表示。

图1-1-8 数控加工适用范围
图1-1-8(a)所示为零件复杂程度及生产批量的不同,三种机床的应用范围的变化。当零件不太复杂,生产批量又较小时,宜采用通用机床。当生产批量很大,宜采用专用机床。而随着零件复杂程度的提高,数控机床越显得适用。目前,随着数控机床的普及,应用范围由BCD向EFG线复杂性较低的范围扩大。
从图1-1-8(b)中可看出通用机床、专用机床和数控机床零件加工批量与生产成本的关系。在多品种、中小批量生产情况下,采用数控机床总费用更为合理。
根据数控加工的优缺点及国内外大量应用实践,一般可按适用程度将零件分为三类。
1.最适用类
(1)形状复杂,加工精度要求高,用通用机床无法加工或虽然能加工但很难保证产品质量的零件。
(2)用数学模型描述的复杂曲线或曲面轮廓零件。
(3)有难测量、难控制进给、难控制尺寸的不开敞内腔的壳体或盒形零件。
(4)必须在依次装夹中合并完成铣、镗、铰或螺纹等多工序的零件。
2.较适用类
(1)在通用机床加工时极易受人为因素(如情绪波动、体力强弱、技术水平高低等)干扰,零件价值又高,一旦质量失控会造成重大经济损失的零件。
(2)在通用机床上加工时制造复杂的专用工装的零件。
(3)需要多次更改设计后才能定型的零件。
(4)在通用机床上加工需要长时间调整的零件。
(5)用通用机床加工时,生产率很低或体力劳动强度很大的零件。
3.不适用类
(1)生产批量大的零件。
(2)装夹困难或完全靠找正定位来保证加工精度的零件。
(3)加工余量不稳定,且数控机床上无在线检测系统可自动调整零件坐标位置的零件。
(4)必须用特定的工艺装备协调加工的零件。
二、控机床的发展方向
目前,我国已有自主版权的数控系统,但绝大多数全功能型数控机床还是采用国外的CNC系统,从机床的整体来看,无论是可靠性、精度、自动化程度和生产效率,与国外相比都还有着不小的差距。
随着科学技术的发展,世界先进制造技术的兴起,对数控加工技术的要求越来越高。如超高速切削,超精密加工等技术的应用,对数控机床的机床结构、主轴驱动、数控系统、伺服系统等提出了更高的性能指标,使数控机床在技术上呈现以下几个方面的发展趋势。
1.高速度
提高生产效率一直是机床技术发展的目标之一,数控机床的出现和快速发展的原因之一,就是生产效率要比普通机床高得多。近年来,数控机床的生产效率又提高了很多,主要方法是减少切削时间和非切削辅助时间。减少切削时间是从提高切削速度,即提高主轴转速来实现的。加工中心的主轴转速已从10年前一般为4000~6000r/min提高到8000~12000r/min,最高的在100000r/min以上,数控车床的主轴转速也提高到5000~20000r/min,磨削的砂轮线速度提高到100~200m/s。
据最新统计,加工中心的切削时间不超过整个工作时间的55%,因此,减少非切削时间是提高生产效率的一个主要手段。非切削时间由两部分组成:一是空行程时间,即快速移动所需的时间;另一个是辅助时间,主要是刀具交换时间和工件交换时间。
要缩短空行程时间,就需要提高快速移动的速度。目前,一般的快速移动速度已达到20~24m/min,有的在30m/min左右,最快的可达60m/min。特别是直线移动进给伺服电动机的出现,为进一步提高移动速度带来了可能。另外,要减少辅助动作的时间,就需要缩短自动交换刀具的时间和自动交换工件的时间。目前,数控车床刀架的转位时间已达到0.4~0.6s,加工中心刀具自动交换时间已达到3s左右,快的可达到1s以内。而加工中心托板交换时间已从过去的12~20s缩短到6~10s,快的已达到2.5s。
现主要从以下几个方面采取措施以提高速度指标:
1)数控系统
微处理器是现代数控系统的核心部件。采用位数、频率更高的微处理器,以提高系统的基本运算速度。目前已由16位CPU过渡到32位CPU,并向64位CPU发展。采用32位微处理器和多微处理器结构,以提高系统的数据处理能力,即提高插补运算的速度和精度。
2)配置高速、功能强大的内装式可编程控制器(PLC)
通过提高可编程序控制器的运行速度,来满足数控机床高速加工的要求。新型的PLC具有专用的CPU,基本指令执行速度可达us/step,可编程步数可扩大到16000步以上,利用PLC的高速处理功能,使CNC与PLC之间能有机结合,满足数控机床运行中的各种实时控制。
3)提高多轴控制水平
新型的数控系统都具有多轴控制功能,可采用多轴联动实现对复杂及特殊型面的加工,还可采用多刀具同时加工的多刀架控制。
4)超高速切削刀具的运用
目前金刚石涂层刀具和陶瓷刀具已在超高速加工中得到应用。
2.高精度
数控机床的高精度,包括高的机床几何精度和高的加工精度,而高的几何精度是提高加工精度的基础。几何精度中最主要的是定位精度,定位精度的提高,加上机床的结构特性和热稳定性的提高,使得数控机床的加工精度得到了大幅度提高。如加工中心的加工精度从过去的±0.01mm提高到±0.005mm,甚至更高。
为实现更高精度的目标,现主要采取以下措施:
1)伺服驱动系统
采用数字式交流伺服系统,在定位精度、进给速度等伺服性能方面较以往模拟式直流伺服系统有极大改进,甚至出现采用直线电动机直接驱动机床工作台的所谓“零传动”直线伺服进给方式,从而极大地提高了加工精度。
2)前馈控制技术
以前的伺服系统是将指令位置和实际位置的偏差乘以位置环的增益,其积作为速度指令,去控制电动机的速度。这种方式总是存在位置跟踪滞后误差,使得在加工拐角或圆弧时加工情况恶化。所谓前馈控制,就是在原来的控制系统上加上速度指令的控制方式,这样使跟踪滞后误差大大减小,以改进拐角切削加工精度。
3)机床静、动摩擦的非线性补偿控制技术
机床静、动摩擦的非线性会导致机床床鞍爬行。除了在机床结构上采取措施降低静摩擦外,新型的数字伺服系统具有自动补偿机械系统静、动摩擦非线性的控制功能。
4)补偿技术的发展和广泛应用
现代数控机床利用计算机数控系统的软件补偿功能对伺服系统进行多种补偿,如轴向运动定点误差补偿、丝杠螺距误差补偿、齿轮间隙补偿、热变形补偿等。
5)高精度的脉冲当量
高精度的脉冲当量可提高定位精度和重复定位精度。
6)采用高分辨率的位置检测装置
例如,高分辨率的脉冲编码器,内装微处理器组成的细分电路,使得分辨率大大提高。
3.高可靠性
现代数控系统采用专用芯片及混合式集成电路,使得系统集成度提高,元器件减少,功耗降低,提高了可靠性。
数控软件的功能更加齐全,带有自诊断及保护功能,提高了加工过程的安全可靠性。
4.高自动化
从数控系统发展到以微处理器为主的CNC系统后,系统的功能得到不断扩大,因此,数控机床的自动化程度也不断提高。除了自动换刀和自动交换工件外,先后出现了如刀具寿命管理、自动更换备用刀具、刀具尺寸自动测量和补偿、工件尺寸自动测量及补偿、切削参数的自动调整等功能,使单机自动化达到了很高的程度。刀具磨损和破损的监控功能也在不断完善。
5.多功能化
1)数控机床采用一机多能,以提高设备利用率
一机多能就是把不同机床的功能集中于一台机床中体现,其典型代表是配有自动换刀机构的各类加工中心,能在同一台机床上同时实现铣削、镗削、钻削、车削、扩孔、铰孔、攻螺纹,甚至磨削等多工序的加工。为了进一步提高功效,现代数控机床又采用了多主轴、多面体切削,即同时对一个零件的不同部位进行不同方式的切削加工,如各类五面体加工中心。另外,现代数控系统的控制轴数也在不断增加,有的多达31轴,同时联动的轴数已达7轴。这种机床有更高的加工精度,还可以大大提高工作效率,节约占地面积、减少设备台数就是节约投资。
2)良好的人机对话功能
在一台机床上可同时进行零件加工和程序编制,即具有前台操作、后台编辑的功能。现代数控系统利用彩色CRT进行二维图形的轨迹显示,更好的还可实现彩色三维动态图形的模拟,显示所编程序的加工轨迹,便于零件程序的调试、修改、确保实际加工过程的安全。
3)更强的通信功能
数控机床由单机发展到FMC、FMS,进而联网形成计算机集成制造系统(CIMS),需要数控系统具有更强的通信功能。大多数控系统都具有RS-232C和RS-422高速远距离串行接口,可以按照用户级的格式要求,同上一级计算机进行多种数据交换。高档的数控系统应具有DNC接口,可以实现几台数控机床之间的数据通信,也可以直接对几台数控机床进行控制。
现代数控机床,为了适应自动化技术的进一步发展,满足工厂自动化规模越来越大的要求,满足不同厂家不同类型数控机床联网的需要,已采用了MAP工业控制网络,现已实现了MAP3.0版本,为现代数控机床进入FMS及CIMS创造了条件。
6.编程自动化
CAM自动编程是当前最先进的数控加工编程方法。目前CAD/CAM图形交互式自动编程软件得到较多的应用,它是利用CAD完成零件几何图形的计算机绘制,再经计算机内的刀具轨迹数据计算和后置处理,而自动生成NC零件加工程序,再通过通信接口传入数控机床进行自动控制加工,从而达到CAD/CAM集成一体化,实现无图纸化设计与制造。另外,随着CIMS技术的发展,当前又出现了CAD/CAPP/CAM集成的全自动编程方式,它与CAD/CAM系统编程的最大区别是其编程所需的加工工艺参数不必由人工参与,而直接从系统内的CAPP(计算机辅助工艺设计)数据库获得。
7.智能化
现代数控系统中,引进了自适应控制技术。自适应控制(Adaptive Control AC)技术是要求在随机变化的加工过程中,通过自动调节加工过程中所测得的工作状态、特性,按照给定的评价指标自动校正自身的工作参数,以达到或接近最佳工作状态的技术。自适应控制技术能根据切削条件的变化,自动调整并保持最佳工作状态,以达到很高的加工精度及较小的表面粗糙度,同时也能提高刀具的使用寿命和设备的生产效率。
智能化的数控系统主要体现在以下几个方面:
(1)刀具寿命自动检测更换 对工件超差、刀具磨损、破损,进行及时报警、自动补偿或更换备用刀具。
(2)自动诊断、自动修复 出现故障时自动诊断、自动修复。
(3)实时补偿 根据加工时的热变形,对滚珠丝杠等部件的伸缩进行实时补偿。
(4)引进模式识别技术 应用图形识别和声控技术,由系统自己辨认图样,按照自然语言命令进行CNC自动加工。
思考与练习
1.数控发展趋势从哪些方面着手?
2.可控制轴与联动轴的区别是什么?